Resources | Technical Documents
WearCheck Knowledge & Expertise
WearCheck has the benefit of a global network of industry knowledge leaders. The following resources are drawn from hundreds of years of their experience in the oil analysis industry. We hope you find these resources helpful in your understanding of oil analysis and provide you with an oil analysis program of increased value.
Technical Documents
Where does all that Metal come From?
Oil analysis involves the extract ion of a small, representative sample of oil from a lubricated piece of machinery and subjecting it to a whole battery of chemical and physical tests in a laboratory. The data is then interpreted to produce a report. There are three fundamental areas of interest in an oil analysis report: the health of the machine being sampled, the health of the oil lubricating that machine and the levels of contamination.
What is RPD ferrography?
Oil analysis, including ferrography, provides the greatest value for money of any maintenance monitoring technique. While most maintenance managers are familiar with the general concept of oil analysis, ferrography is less understood. This Technical Bulletin describes how ferrography fits into the overall oil analysis picture, with particularly emphasis on RPD (rotary particle deposition) ferrography and how it can be integrated into a maintenance programme to achieve substantial financial benefits at relatively low cost.
Oil pressure mapping to measure bearing wear
One of the current buzzwords being used in condition monitoring is oil pressure mapping. This technical bulletin explains oil pressure mapping, why this diagnostic technique was developed and how it is used to measure engine bearing wear.
Wear limits versus trends
Common questions asked by people using oil analysis are `What wear limits do you use?", "What levels are normal?", and "What levels are abnormal?" These are not unreasonable questions. A number of OEM"s (original equipment manufacturers) do have wear limits for their equipment but unfortunately they are not an effective means of determining the health of a component. The levels of contamination and particularly wear debris in an oil sample are dependent on too many factors for an equipment manufacturer to set out nice, neat wear tables that say, for example, 0 - 50 is okay, 50 - 100 indicates a problem, and over 100 is very serious. This runs the risk of saying that 49 `whatevers" is acceptable and 51 is not when, in this case, there is only a difference of 4%.
Debris Analysis
The wear readings traditionally encountered in oil analysis are expressed as a percentage, or more commonly as PPM (parts per million) with 1 PPM being equal to 1/10000th of 1% (eg. Fe = 100 PPM). These concentrations are measured with a spectrometer, in Wearcheck’s case an ICP (Inductively Coupled Plasma) spectrometer. There is a fundamental limitation to measuring the concentration of wear debris with this technique. Because of the way that these instruments work, particles greater than 8 - 10 m (micron) cannot be detected. It is obvious that a critical wear situation could exist with large particles present but the iron concentration might be low, i.e. most of the wear particles are greater than 10 m in size and would not be picked up by the spectrometer.
Technical Documents Categories
Resource Categories
Oil analysis involves the extract ion of a small, representative sample of oil from a lubricated piece of machinery and subjecting it to a whole battery of chemical and physical tests in a laboratory. The data is then interpreted to produce a report. There are three fundamental areas of interest in an oil analysis report: the health of the machine being sampled, the health of the oil lubricating that machine and the levels of contamination.
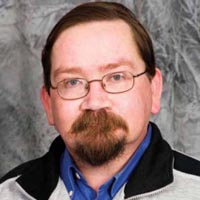
John Evans
WearCheck Africa
Oil analysis, including ferrography, provides the greatest value for money of any maintenance monitoring technique. While most maintenance managers are familiar with the general concept of oil analysis, ferrography is less understood. This Technical Bulletin describes how ferrography fits into the overall oil analysis picture, with particularly emphasis on RPD (rotary particle deposition) ferrography and how it can be integrated into a maintenance programme to achieve substantial financial benefits at relatively low cost.
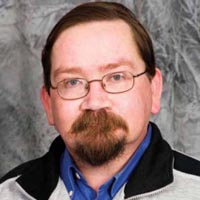
John Evans
WearCheck Africa
One of the current buzzwords being used in condition monitoring is oil pressure mapping. This technical bulletin explains oil pressure mapping, why this diagnostic technique was developed and how it is used to measure engine bearing wear.

Gary Blevins
WearCheck Africa
Common questions asked by people using oil analysis are `What wear limits do you use?", "What levels are normal?", and "What levels are abnormal?" These are not unreasonable questions. A number of OEM"s (original equipment manufacturers) do have wear limits for their equipment but unfortunately they are not an effective means of determining the health of a component. The levels of contamination and particularly wear debris in an oil sample are dependent on too many factors for an equipment manufacturer to set out nice, neat wear tables that say, for example, 0 - 50 is okay, 50 - 100 indicates a problem, and over 100 is very serious. This runs the risk of saying that 49 `whatevers" is acceptable and 51 is not when, in this case, there is only a difference of 4%.
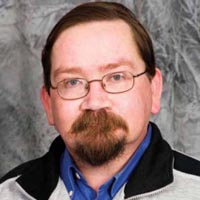
John Evans
WearCheck Africa
The wear readings traditionally encountered in oil analysis are expressed as a percentage, or more commonly as PPM (parts per million) with 1 PPM being equal to 1/10000th of 1% (eg. Fe = 100 PPM). These concentrations are measured with a spectrometer, in Wearcheck’s case an ICP (Inductively Coupled Plasma) spectrometer. There is a fundamental limitation to measuring the concentration of wear debris with this technique. Because of the way that these instruments work, particles greater than 8 - 10 m (micron) cannot be detected. It is obvious that a critical wear situation could exist with large particles present but the iron concentration might be low, i.e. most of the wear particles are greater than 10 m in size and would not be picked up by the spectrometer.
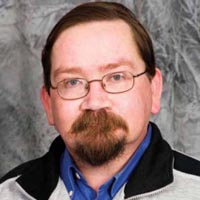